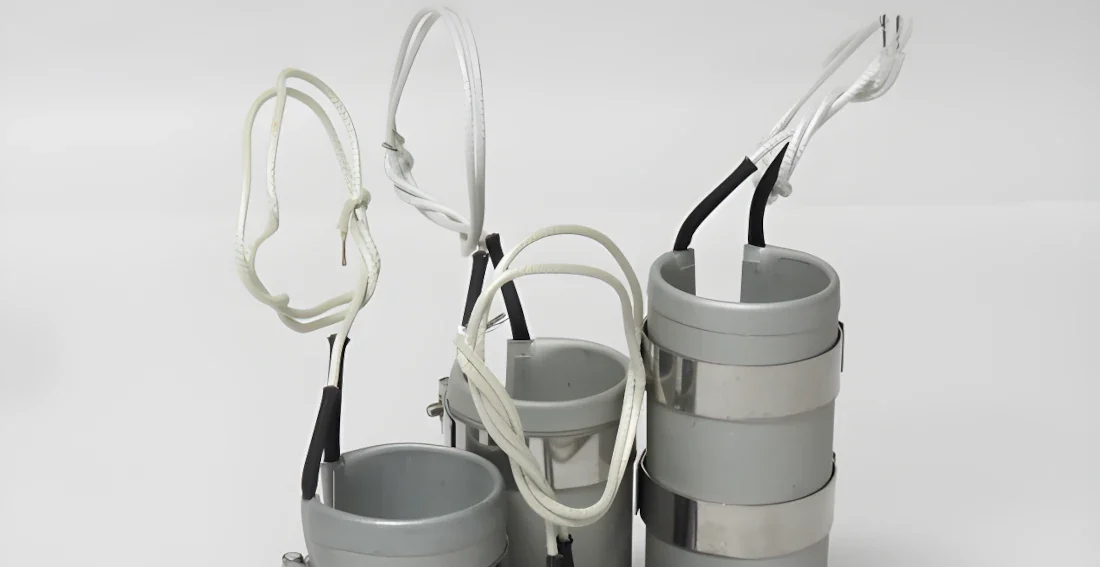
How to Configure a Custom Nozzle Heater
Nozzle heaters are needed to maintain precise temperature control in applications such as injection molding and extrusion, where even minor temperature deviations can impact product quality. Because different processes and materials have unique heating requirements, customization is vital to ensure optimal performance and efficiency, as well as consistent product quality.
Keep reading to learn more about the factors you need to consider when configuring your custom nozzle heater.
1. Diameter
Choosing the correct diameter ensures your nozzle heater can effectively transfer heat while reducing energy wastage. Hi-Watt offers several diameter options from 3/4” and below to 3”-plus. Please contact our team at sales@hiwattinc.com or (800) 321-8007 for a complete list of our diameter options.
To determine the diameter, measure the outer dimension of the nozzle where the heater will be installed. Your chosen diameter must match the nozzle’s dimensions as closely as possible.
2. Width
The width of the heater will determine its coverage area, impacting how heat is distributed along the length of the nozzle. When measuring width, you’ll want to measure the length of the nozzle area that needs heating. Similar to diameter, you’ll want to choose a width that closely matches the length of the nozzle area. Hi-Watt can configure nozzle heaters in a variety of widths. Please contact our team at sales@hiwattinc.com or (800) 321-8007 to learn more.
3. Voltage
Next, you need to configure the voltage requirement to ensure the heater operates efficiently and safely within the system’s electrical capabilities. The required voltage depends on the specific application’s power supply and the operational environment.
4. Target Wattage
Your target wattage is based on your application, the material being heated, and the environmental conditions the heater will be exposed to. When calculating wattage, use the basic heat transfer formula, considering factors such as target heating temperature, ambient temperature, the surface area of the nozzle that needs heating, and the material being heated.
Calculating target wattage can be complicated—for better accuracy, we recommend contacting Hi-Watt’s application specialists at (800) 321-8007.
5. Lead Length & Type
The lead length must be sufficient to allow your heater to connect to the power source without tension or excessive slack, which causes potential damage over time. When determining lead length, measure the distance from the power source to the location of the heater, considering the path the leads will take to avoid any obstructions or potential hazards.
When choosing a lead type, you’ll have three primary options to choose from:
- 22 ga 550C Hi-Temp: This lead type can withstand temperatures up to 550 degrees Celsius (1,022 degrees Fahrenheit), making them ideal for applications requiring high heat resistance.
- 20 ga Braided Silicone Rubber: This lead type is covered with a silicone rubber sheath, which provides good heat resistance and insulation. Braided silicone rubber leads are suitable for moderate temperatures and provide excellent flexibility and durability.
- 18 ga Braided Silicone Rubber: This option is similar to the 20 ga but has a thicker gauge. It offers more durability and a slightly higher current capacity, making them more suitable for applications requiring more robust handling and where the heater draws higher currents.
Consider a stainless steel braid if your leads need extra protection against mechanical damage, abrasion, or harsh environmental conditions such as corrosive chemicals or moisture. The stainless steel braid protects the wires while maintaining flexibility, which is critical in dynamic applications where the heater may move or vibrate.
6. Process Temperature
Nozzle heater manufacturers and suppliers will also need to know your process temperature for multiple reasons:
- It impacts material selection. For example, high process temperatures may require using more heat-resistant materials like high-grade stainless steel or nickel alloys for both the sheath and the internal heating elements.
- Determining which safety features, like thermal fuses, thermostats, or thermocouples, may be needed to monitor and control the heat output effectively.
- Understanding what type of insulation and wiring is needed. Higher process temperatures require high-temperature insulation and wiring, such as Teflon or fiberglass, to withstand the operational environment without degrading.
7. Other Customization Options
Depending on your application, you could request other special features, including:
- Integrated temperature sensors (for precise temperature monitoring and control)
- Cooling tubes (for applications that involve high-temperature cycles followed by rapid cooling)
- Zoned heating (for applications where uniform heat distribution is challenging or where different areas of the process require different temperatures)
- Explosion-proof designs (for hazardous environments, such as in chemical processing)
- Corrosion-resistant materials and watertight seals (for environments prone to moisture or corrosive chemicals)
- Clamping mechanisms (to improve the heater’s contact with the nozzle)
- High-precision machining (for complex or miniaturized components)
Start Configuring Your Nozzle Heater Today
Find the right nozzle heater with help from Hi-Watt. Based in Michigan, we’re a regional supplier of industrial heating solutions. Visit our website to browse our stock options or customize your own with our easy-to-use configurator. If you need help customizing your nozzle heater, please contact one of our product specialists.